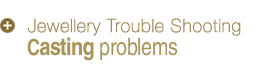 |
Blisters / Spalling |
 |
Nguyên nhân |
Khắc phục |
Quá trình hấp sáp không đủ. |
Tăng thời gian hấp lấp lâu hơn ở nhiệt độ giữa 160 - 220ºC (ít nhất khoảng 3.5 giờ) |
Hấp sáp trong láp ở nhiệt độ quá cao. |
Phụ thuộc vào quá trình cài đặt nhiệt độ hấp sáp. (theo biểu đồ burn out) |
Đặt láp vào lò nung quá sớm. |
Để láp đứng yên khoảng 1 giờ trước khi đưa vào lò hấp sáp để đảm bảo độ cứng của thạch cao. |
Láp quá nóng trong quá trình hấp. |
Nhiệt độ của láp không vượt quá 740ºC. |
Bubbles/incomplete spheres (bị bọt khí) |
 |
Nguyên nhân |
Khắc phục |
Do điện sử dụng hoặc sáp bị dơ, nhiễm bẫn. |
Sử dụng sáp sạch, phải đảm bảo sáp hoàn toàn khô trước khi đưa vào đúc. |
Do máy hút chân không. |
Kiểm tra lại máy hút chân không |
Hút chân không không đủ trong quá trình trộn tay. |
Tăng thời gian hút chân không. |
Thời gian trộn quá dài, thạch cao đã cứng nhanh trong quá trình hút chân không. |
Đảm bảo phải trộn theo chỉ dẫn (thời gian tối đa: 8 phút). |
Sai tỷ lệ nước; quá ít nước. |
Sử dụng tỷ lệ thạch cao : nước theo chỉ dẫn. |
Nhiệt độ của hỗn hợp trộn quá cao. |
Nhiệt độ tối ưu của hỗn hợp từ 20-22ºC, sau quá trình hút chân không |
Rough surfaces
(bề mặt nhám) |
 |
Nguyên nhân |
Khắc phục |
Nhiệt độ láp quá cao trong suốt quá trình hấp. |
Nhiệt độ của láp không vượt quá 740ºC. |
Thời gian làm việc không đủ. |
Đảm bảo phải trộn theo chỉ dẫn (thời gian tối đa: 8 phút). |
Nhiệt độ kim loại quá cao. |
Giảm nhiệt độ đúc kim loại. |
Chất lượng sáp quá xấu. |
Sáp phải được làm sạch vào láng bóng. |
Hấp sáp ướt quá lâu hoặc nhiệt độ, áp suất quá cao. |
Hấp sáp ướt tối đa 1 giờ tại áp suất không khí. |
Hấp sáp quá nhanh. |
Để láp ít nhất 1 giờ để đảm bảo độ cứng trước khi hấp sáp. |
Nhiệt độ lò hấp sáp quá cao. |
Theo qui trình nhà cung cấp đưa ra. |
Non or partial fill (không điền đầy) |
 |
Nguyên nhân |
Khắc phục |
Nhiệt độ kim loại hoặc nhiệt độ của láp quá thấp. |
Tăng nhiệt độ đúc kim loại trước khi tăng nhiệt độ láp từ lò nung. |
Quá trình hấp chưa hoàn tất. |
Tăng thời gian hấp ít nhất 4.5 giờ ở 740ºC. |
Cuống phun đặt sai vị trí. |
Tăng kích thước cuống phun, bề dày ít nhất hơn 25% bề dày của sản phẩm. |
Tốc độ đúc bằng máy quay quá chậm. |
Tăng tốc độ lên |
Hút chân không yếu khi đúc có hút chân không. |
Kiểm tra bơm chân không. |
Porosity / Gas (rổ bề mặt) |
 |
Nguyên nhân |
Khắc phục |
Nhiệt độ kim loại quá cao. |
Giảm nhiệt độ đúc kim loại. |
Nhiệt độ láp quá cao trong suốt quá trình hấp. |
Nhiệt độ của láp không vượt quá 740ºC. |
Quá trình hấp chưa xong. |
Tăng thời gian hấp ít nhất 4.5 giờ ở 740ºC. |
Kim loại không sạch. |
Không sử dụng nhiều hơn 50% hợp kim tái sử dụng và đảm bảo phải sạch sẽ. |
Cuống phun không chính xác. |
Tăng kích thước cuống phun, bề dày ít nhất hơn 25% bề dày của sản phẩm. |
Flashing/Finning (bavia) |
 |
Nguyên nhân |
Khắc phục |
Tỷ lệ nước và thạch cao. |
Đo chính xác tỷ lệ nước và thạch cao theo chỉ dẫn của nhà cung cấp |
Nhiệt độ láp quá cao từ trong lò hấp. |
Quan sát nhiệt độ của từng kim loại để điều chỉnh hợp lí. |
Di chuyển láp quá sớm. |
Để láp đứng yên 1 giờ sau khi đổ thạch cao xong. |
Vật liệu đúc với áp lực quá lớn. |
Giảm áp lực nén khi đúc ở máy đúc có hút chân không. |
Thời gian đông đặc của thạch cao không đủ. Đảm bảo phải trộn theo chỉ dẫn (thời gian tối đa: 8 phút). |
Đảm bảo phải trộn theo chỉ dẫn (thời gian tối đa: 8 phút). |
Thạch cao và nước quá lạnh. |
Đảm bảo nhiệt độ hỗn hợp trộn không ít hơn 21ºC sau khi hút chân không. |
Láp không được điền đầy ở đỉnh do tăng lực ép khi đúc. |
Đảm bảo láp đã được điền đầy đến đỉnh khi đúc, tối thiểu 2 cn từ đỉnh cây sáp đến đỉnh của láp. |
Khuôn không khô trước khi hấp. |
Giữ khuôn khô ráo cho đến khi đem đi hấp. |
Kết nối giữa cây sáp và miếng gá bằng cao su bị tách ra trong quá trình đông đặc. |
Đáy cây sáp phải dính chặt vào gá đỡ cao su. Nếu thấy cần thiết có thể hàn bằng sáp nóng chảy vào gá đỡ cao su.. |