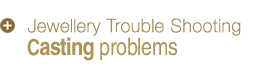 |
Problem Flashing or Finning |
 |
Cause |
Remedy |
Incorrect powder/water ratio (too much water) |
Use correct amount of water (especially important with vacuum investing machines) |
Work time of investment too long. Slurry start to set while still under vacuum. |
Ensure the work time is fully used. Normally 8 minutes. |
Casting the material with too much force. |
For centrifugal casting, use the correct spin For vacuum casting, reduce pressure. |
Moving flask too soon |
Leave the flasks for at least 1 hour. |
Moulds allowed to dry out before burn out. |
If not burning out the same day, keep moulds wet by covering with wet sacking. |
Flasks overheated during burn out. |
Ensure maximum burn out temperature
does not exceed 750 °C |
Bubbles |
 |
Cause |
Remedy |
Investment too thick. Too little water. |
Use correct powder/water ratio. |
Vacuum pump/tank faulty. |
Ensure equipment is regularly serviced
and adequate for the task. |
Water marking |
 |
Cause |
Remedy |
Incorrect powder/water ratio (too much water) |
Use correct amount of water (especially important with vacuum investing machines) |
Work time of investment not used up. |
Ensure the work time is used up and slurry temperature is 20 - 30 °C. |
Investment powder expired(too old) |
Do not keep investment too long time. |
Blister |
 |
Cause |
Remedy |
Dewax soak time not long enough. |
Extend time for dry dewax at least 3 hours
(temperatures between 150 to 250°C) |
Flasks dewaxed at too high temperature. |
Do not exceed 250 °C during dry de-wax.
Wax will boil and erode investment surface. |
Flasks put in furnace too soon after investing. |
Leave flasks undisturbed for a minimum of
one hour before de-wax. |
Rough surfaces |
 |
Cause |
Remedy |
Rough waxes. |
Use too much powder on the rubbers. |
Flasks dewaxed at too high temperature. |
Do not exceed 250°C during dry de-wax.
Wax will boil and erode investment surface. |
Steam de-wax for too long. |
Steam, de-wax for a maximum of 1 hour.
Steam will erode surface of the casting. |
Flasks overheated during burn out. |
Ensure maximum burn out temperature
does not exceed 750 °C |
Metal temperature too hot. |
Reduce metal casting temperature. |
Gas porosity |
 |
Cause |
Remedy |
Usage of low quality metal. |
Do not use more than 50% recycled alloy and ensure it is clean. |
Reaction with investment temperature. (Flask temperature too hot) |
Reduce flask temperature down, Specially on big design. |
Overheating the metal. |
Reduce metal casting temperature. |
Temperature inside furnaces over. |
Ensure the quality of Thermocouple can control temperature. |
Shrinkage porosity |
 |
Cause |
Remedy |
Incorrect spruing |
Sprues should be attached to the heaviestpiece of the casting. There should be sufficient sprues to ensure the casting is adequately fed. |
Flask temperature too cold. |
The flask temperature should be just hot enough to achieve complete fill. |
Incomplete casting |
 |
Cause |
Remedy |
Metal or flask temperature too cold. |
Increase casting temperatures. If the metal or flask is too cold, the metal will freeze before completely filling the mould. |
Improperly sprued. |
the sprue system should be designed to allow the metal to enter easily and without restriction. |